汽车市场竞争中,汽车零部件的质量和性能至关重要。为了满足不断提高的市场需求,汽车零部件设计仿真一体化解决方案一经提出,得到了行业内的认可,下面就来详细介绍汽车零部件设计仿真一体化解决方案是怎么样的?
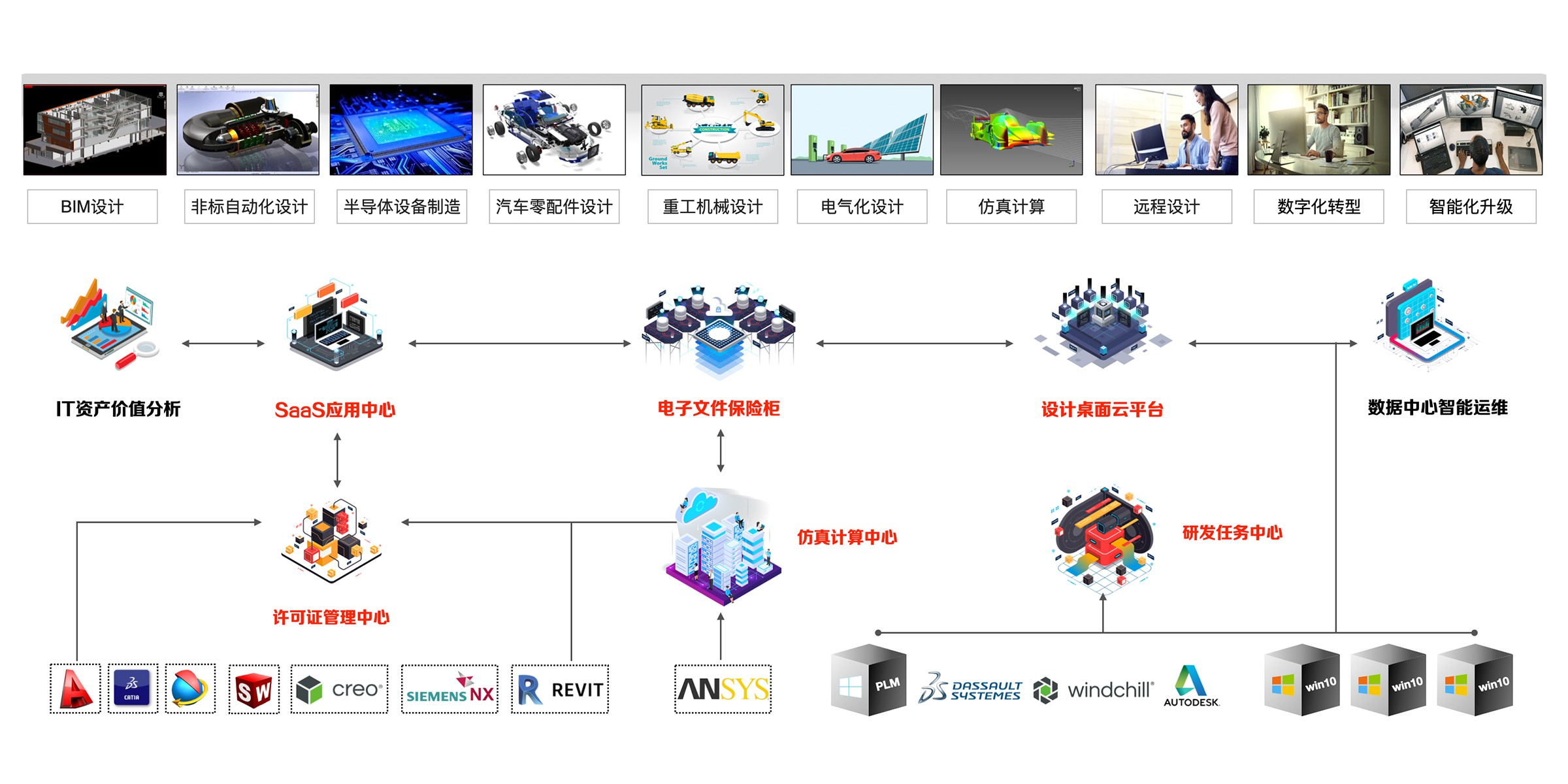
一、需求背景
目前,消费者对汽车的安全性、舒适性、可靠性和燃油经济性等方面的要求越来越高。同时,汽车制造商也面临着缩短产品开发周期、降低成本和提高产品质量的巨大压力。传统的汽车零部件设计方法往往依赖于经验和试验,这种方法不仅成本高、周期长,而且难以准确预测零部件的性能和可靠性。因此,需要一种更加高效、准确的设计方法,即汽车零部件设计仿真一体化解决方案。
二、解决方案概述
汽车零部件设计仿真一体化解决方案是将设计和仿真两个环节紧密结合起来,实现从设计到仿真的无缝衔接。该解决方案采用先进的计算机辅助设计(CAD)和计算机辅助工程(CAE)技术,通过建立数字化的设计模型和仿真模型,对汽车零部件的性能和可靠性进行预测和优化。
三、设计环节
需求分析
在设计之前,首先要对汽车零部件的需求进行深入分析。这包括了解零部件的功能、性能要求、安装位置、工作环境等因素。通过需求分析,可以为后续的设计工作提供明确的目标和方向。
CAD设计
采用先进的CAD软件,进行汽车零部件的三维设计。设计师可以根据需求分析的结果,快速创建出零部件的几何模型。在设计过程中,可以随时对模型进行修改和优化,以满足不同的设计要求。
设计验证
设计完成后,需要对设计结果进行验证。这可以通过与现有的零部件进行对比、进行虚拟装配等方式来实现。如果发现设计存在问题,可以及时进行修改,避免在后续的制造环节中出现问题。
四、仿真环节
建立仿真模型
根据设计好的CAD模型,建立相应的仿真模型。仿真模型可以包括力学模型、热学模型、流体力学模型等,具体取决于零部件的性能要求。
仿真分析
利用CAE软件对仿真模型进行分析,预测零部件的性能和可靠性。例如,可以进行强度分析、疲劳分析、热分析、流体分析等。通过仿真分析,可以发现设计中存在的潜在问题,并提出相应的优化方案。
优化设计
根据仿真分析的结果,对设计进行优化。优化可以包括改变零部件的几何形状、材料选择、加工工艺等。通过不断地优化设计,可以提高零部件的性能和可靠性,同时降低成本。
五、一体化优势
提高设计效率
设计仿真一体化解决方案可以实现从设计到仿真的无缝衔接,减少了设计和仿真之间的重复工作,提高了设计效率。设计师可以在设计过程中随时进行仿真分析,及时发现问题并进行优化,避免了在制造环节中出现问题后再进行修改的情况。
提高设计质量
通过仿真分析,可以准确预测零部件的性能和可靠性,为设计提供科学依据。设计师可以根据仿真结果进行优化设计,提高零部件的质量和性能。同时,一体化解决方案可以减少人为因素对设计的影响,提高设计的准确性和可靠性。
降低成本
传统的设计方法往往需要进行大量的试验和验证,成本较高。而设计仿真一体化解决方案可以通过虚拟仿真代替部分物理试验,降低了试验成本。同时,优化设计可以提高零部件的性能和可靠性,减少废品率和维修成本。
总之,汽车零部件设计仿真一体化解决方案是一种高效、准确的设计方法,可以帮助汽车制造商提高设计效率、质量和降低成本。